Now that the first implementers of the new global Health & Safety (H&S) standard, ISO 45001, have moved through the process, Gay Sutton takes a closer look. What is involved, how do you go about it… and how does it benefit your materials handling business?
Companies implementing the global quality management system standard ISO 9001, or the environmental management system standard ISO 14001, will be aware of the many ongoing benefits accredited certification can deliver. Now it is the turn of occupational health and safety, for which international standard ISO 45001 was published last year in March 2018.
Overview
“ISO 45001 provides a framework and tool for organisations to follow to implement effective health and safety,” says Kate Field, Global Product Champion for Health and Safety at business improvement company BSI, who has over 18 years experience in OH&S, covering most industry sectors. “The focus is very much on prevention of injuries and ill-health, and encouragingly, the provision of a healthy workplace.”
“ISO 45001 is about best practice and provides a robust framework that can be consistently applied. Not only can it reduce the occurrence of accidents and incidents, but it also reduces things like sickness absence rates. There is also good evidence to show that where organisations get it right, it improves recruitment and retention, and results in a more loyal and productive workforce.”
For materials handling companies considering adopting the standard, Kate advises, “The main thing is not to be scared by it. Many of the elements will already be in place, such as risk assessments and mechanisms for talking and engaging with the workforce.
“ISO 45001 is an outcome-based management system and is designed to be proportionate to the size and nature of the business…It’s designed to fit your needs and help you best manage occupational health and safety.”
Already the first implementers have moved through the process. So now that it is settling in, what does it entail and what are the benefits?
What’s involved - Key elements
To move to ISO 45001 compliance, Kate explains that there are 5 broad areas to focus on: leadership, culture, design, worker participation and consultation, and the supply chain.
Leadership and culture: There is a strong focus on the role of top management in driving occupational health and safety improvement. “And that’s around creating a culture that supports positive occupational health and safety. So, it needs much stronger ownership by top management.”
Design: ISO 45001 focuses on prevention, particularly at the design stage. “This ensures that the proactive identification of hazards and risks begins at the conceptual design stage, and this can be in the design of the workplace facility, the product or the organisation. If you can design hazards out, then you make your life easier.”
Worker participation: The new standard recognises that good engagement by the workforce brings measurable H&S benefits as well as improvements in quality and output. It identifies some very specific areas where workers at all levels must be consulted, and then participate in the decision-making.
Supply chain: It focuses on understanding the risks and hazards that can be introduced by the supply chain, and how to manage them. It covers all aspects of interaction with suppliers and contactors, from the materials and products they use to their presence and behaviour on site.
Accredited certification – step by step
Initial step: For anyone interested in moving towards ISO 45001, Kate advises that the first step is to buy a copy of the standard so that organisations can decide on whether they simply use elements of it as a tool to help them or meet the requirements in full and gain accredited certification.
Preparation and planning: The logical place for any materials handling company to start is with a gap analysis. “Look at the systems and processes you already have in place and analyse the changes you need to make to meet the full requirements of the standard. From that you can draw up a step-by-step action plan that prioritises and tackles the areas you need to address.”
Training: Kate advises thinking about the training and competency of your staff and arranging programmes to enable staff to reach the levels of knowledge needed. “You will need to train people in the business to undertake internal audits. There will be a range of other skills and competencies required throughout the business, although some of them may already be in place because of the rigorous EU legislation.”
Accredited certification: Finally, once the company has worked through the action plan and internal audits, it is ready to go for accredited certification. An accredited certification body can get the process in motion.
“Accredited certification is then a two-stage process,” Kate comments. “We (BSI), or another accredited certification body, will audit the organisation to see if it meets the requirements. Once we are happy it does, then we will award accredited certification.”
What challenges should you look out for?
The experiences of companies going through the ISO45001 accredited certification process so far have varied depending on the size and nature of the organisation and their starting point. Kate reports that some distinct trends are emerging:
- Role of top management: There can be challenges in ensuring engagement by the top management. ISO 45001 requires that everyone at the top, from the CEO and HR director to the finance director, has a role in creating a positive culture for health and safety. “This has been quite a change for some organisations. But once they understand the reasons why this should happen, and the benefits it brings, we do see these changes take place.”
- Participation and consultation: There are some very specific things that the ‘non-managerial’ workforce has to be consulted on. They will be asked about their views and must then be involved in the decision-making. “Some organisations have had to work hard to demonstrate that they’re fulfilling these specific requirements,” Kate warns.
- Competency: There has been a trend around organisations demonstrating that they have the right competencies at the right levels on health and safety. There must be evidence that the correct skill sets are in place.
- Taking action: “Organisations carry out their internal audit and identify actions but are not always able to demonstrate they’ve done anything to correct the issues. What often happens is that organisations don’t address the root causes. They address the immediate problem but then see the same problem turn up again at the next audit,” Kate explains.
The benefits - Driving up performance
ISO 45001 is about best practice. So whilst some of these difficulties have revolved around documenting analysis of shortfalls, and the steps taken to address them, it is an iterative process based on the Plan-Do-Check-Act cycle and is designed to lead to a culture of continuous improvement.
“It’s not a static one-off exercise,” Kate concludes.
“It’s about driving up performance and continually looking for opportunities to improve safety and health within the workplace.”
There are advantages to be gained internally, in terms of management improvements and productivity gains, and externally, in corporate reputation and supply chain competitiveness. So, whether a company is aiming to adopt the standard in full, apply elements of it to the entire organisation, or focus on a site or work stream, it will no doubt bring significant benefits that continue to accrue over time.
If you would like to read the unabridged article by Gay Sutton, please visit Eureka, the online magazine for the materials handling professional: http://eurekapub.eu/health-safety/2018/11/01/lift-yourself-to-the-next-…
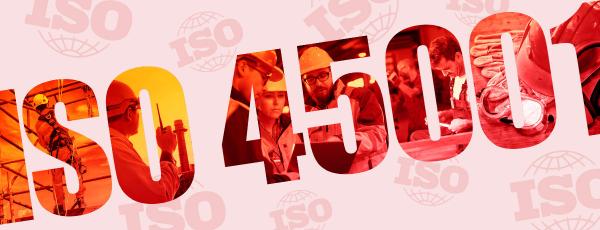
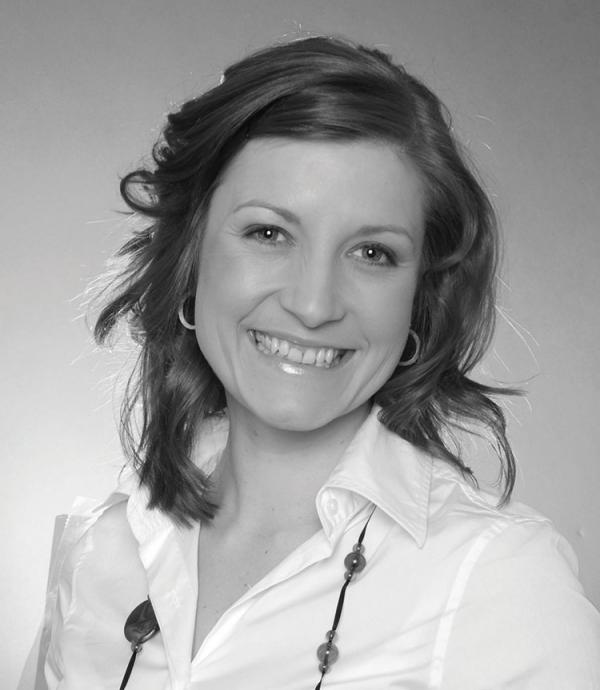