A warehouse is a hectic place at the best of times, with lots of people, vehicles and equipment constantly on the go – taking in stock, fulfilling orders and delivering them out to customers. If a warehouse is not well organised, it can disrupt the operational flow and efficiency of the supply chain as well as affecting profitability.
So just how do you keep your warehouse management under control so it’s clean and well organised? How do you know it’s ready to receive stock, prepare orders, load and ship containers and keep customers happy?
One way of achieving an orderly warehouse is to adopt the 5S model. This model (or system) is a structured programme used to implement workplace organisation and standardisation. The 5Ss represent five disciplines for maintaining a clean and organised workplace that gives a good impression. But having a clean, orderly warehouse isn’t just about looking good: it’s about having more efficient operations, excelling at training and communications and, ultimately, saving time and money. A warehouse operation using the 5S system can quickly identify problems and solve them, and so prevent recurrence.
As well as benefiting staff by making the warehouse a safer, cleaner and more pleasant place to work, the 5S model will also benefit your business by improving work efficiency and productivity, eliminating waste and saving on warehouse operation costs.
Here’s a look at the 5Ss in turn and how they can each contribute towards better warehouse management.
STAGE ONE: SORT
The first S focuses on eliminating unnecessary items and clutter from your warehouse and only keeping what’s necessary. This avoids needless build-ups of stock, wasted time looking for parts, tools and products, and creation of safety hazards resulting from clutter.
This stage will require cleaning up all work areas to make what you have more visible. By removing dirt, debris, oil, broken tools, excess stock and scrap, you will also be able to identify and return items that have been displaced or uncover areas of space that can be used for other purposes.
STAGE TWO: SET IN ORDER
‘A place for everything and everything in its place.’ Setting everything in order means creating useful, effective storage methods. It’s perhaps the most challenging aspect of the 5S system, as streamlining or organising your warehouse operation can take up a lot of time and there is no one-size-fits-all solution. The way you structure your warehouse will depend on how and what it’s used for and how the warehouse processes flow.
STAGE THREE: SHINE
‘Shine’ refers to keeping everything clean and tidy so that no litter or dirt is found in the warehouse. For this stage of the 5S model, an overall clean-up of the warehouse is required. It will include cleaning the whole building, shelves and racking, as well as tools, equipment and machinery. This will make your warehouse management easier and create a more welcoming, safer place for staff to work in, as there will be fewer hazards within it.
STAGE FOUR: STANDARDISE
Set your standards high! This stage in the 5S system is about establishing consistency in the way your warehouse operates, and how tasks are carried out. Implementing a daily routine and a structured way of working will not only help with creating a more efficient and productive environment but will also help your workers appreciate the standards you want to achieve.
Establishing a set of procedures, schedules and checklists that are readily available, visible and easily followed will help staff to understand what needs to be done, and how and when they’re required to do it. Additionally, putting in place appropriate ongoing training and performance evaluation will also give your workers a clearer understanding of what’s expected and so help maintain and improve standards.
STAGE FIVE: SUSTAIN
The final stage of the 5S system relates to sustainability. It’s about sustaining the habit of maintaining and improving standards, so you don’t let all your hard work go to waste. This is the most difficult part to implement as it’s very easy to slip back into old habits. Creating a schedule for regular monitoring and evaluation of your warehouse operation, including a cleaning and clearing rota for staff, will help prevent the build-up of clutter and dirt again. By involving your workforce, you can create a constant reminder of the importance of the 5S model and the standards you expect.
There are plenty of articles on warehouse management to read in our blog section that complement this topic, including the following:
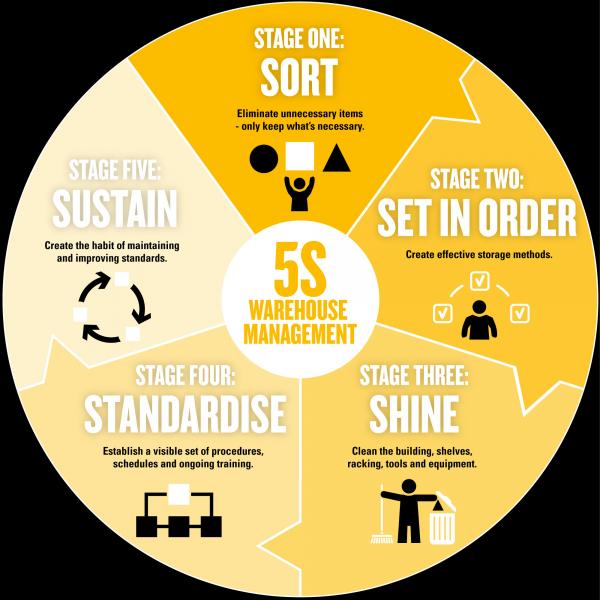
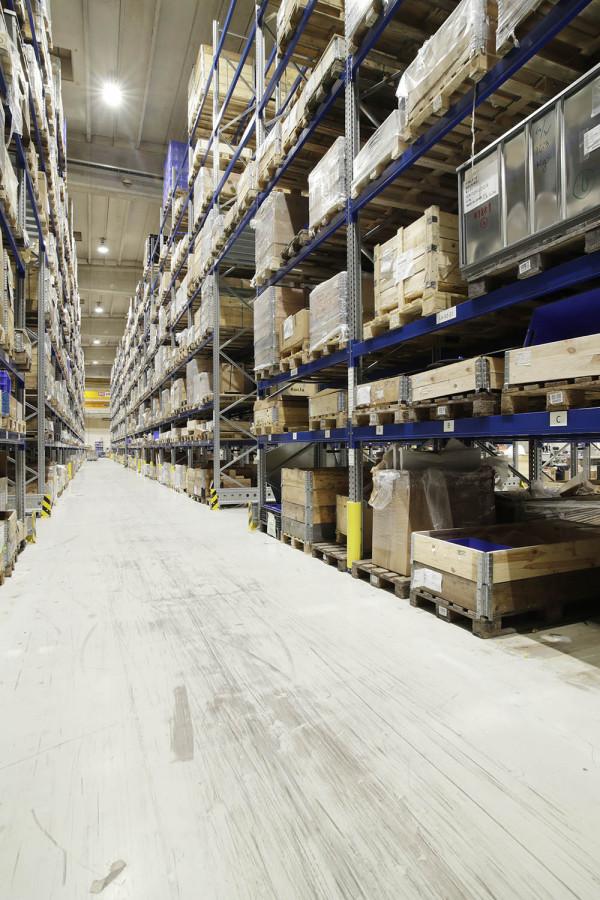